Lithium: How the Future of Transportation Depends on One Key Element
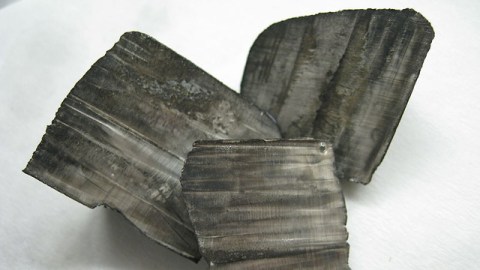
Yesterday, President Obama traveled to Holland, Michigan, a city on the western shore of the state’s Lower Peninsula, to attend the groundbreaking for a factory that will manufacture high-grade lithium-ion batteries for cars and trucks. The visit highlighted the high expectations in the auto industry that battery-powered vehicles such as the Chevy Volt will revive the industry, add jobs, and reduce demand for oil.
Yet what will determine the success of these battery-powered vehicles, independent of such expectations, is one little-understood resource: Lithium. The future of these vehicles is directly linked to this shiny metal and to the relatively low-tech methods of collecting it. Here is what you need to know about this element that so many people are now depending on:
Lithium is found everywhere on earth, but it is found in economic concentrations only in certain parts. As the first metal on the periodic table, it is ideal for batteries because it has the highest energy available per unit of weight.
The lithium in batteries that power everything from laptops and iPods to full-sized cars largely comes from mineral-rich brine, a water-based slurry of compounds found a few meters under otherwise barren deserts and dried-out lakebeds in places such as Chile, Argentina, Bolivia, and parts of the American west.
Lithium is extracted from brine by pumping it into a series of ponds that concentrate the solution through evaporation and through the addition of chemicals that precipitate out unwanted elements.
“It’s really a very simple process once the evaporation ponds have been established: drill a hole at an optimal location, stick a pump in the brine and pump it into the first series of evaporation ponds.” Brian Jaskula, a lithium specialist with the U.S. Geological Survey, told Big Think.
By the time the brine gets to the very last evaporation pond, the lithium concentration has increased to about six percent of the solution, the maximum amount it can be concentrated to. It can then be pumped into tanker trucks and sent off to a processing facility where soda ash and other chemicals are added to turn it into lithium carbonate, which is used to make batteries.
Even under ideal conditions, the evaporation process can take upwards of eighteen months. Geography and climate are critical, since high altitude, rain and humidity, cool winds and lower temperatures can prolong the process and increase the cost.
“There is nothing really high-tech about it at all,” said Jaskula, “it is just using the power of the sun along with the use of pumps and additional chemicals. It is low-tech and a relatively inexpensive way to produce high-quality, battery-grade lithium carbonate compared to a typical hard rock mining operation that requires a lot of heavy equipment.” He added that while evaporation is relatively low-tech to hard rock mining it is nonetheless a time- and knowledge-intensive process.
The U.S. has only one working brine site, operated by the company Chemetall Foote at a lakebed in Silver Peak, Nev., roughly halfway down the state’s diagonal southern border. Forty years ago, Silver Peak was a pioneer in extracting lithium from brine, and continues to produce now.
“Over the past decade the demand for lithium has grown six to eight percent per year, consistently, with the exception of last year which was a tough and unusual year,” said Timothy McKenna, a spokesperson for Chemetall’s parent company Rockwood Holdings.
Despite a surplus of lithium now on the market, expectations for an increase in demand run high, particularly as battery-driven transportation takes off: “While the laptop computer might have an ounce of lithium in its battery, a car battery is going to have twenty-five to forty pounds, so the magnitude is huge,” said McKenna.
The Silver Peak operation is expanding with a grant from the Department of Energy. And as Jaskula explained, “There are other companies right now actively exploring areas close to it. Nevada especially has quite a bit of potential for other brine locations.”
Unrealized lithium-rich deposits exist elsewhere as well. Landlocked Bolivia, for instance, has more lithium than Chile, with roughly nine million metric tons under the ground to Chile’s seven-and-a-half million, according to Jaskula. However a raft of issues has stymied development in Bolivia, including the decision to use national-led production over foreign-backed investment, disputes with neighboring countries, and a lack of the infrastructure necessary to collect and transport the metal to market in large quantities.
Following a recent discovery signaling a wealth of minerals and metals, Afghanistan also seems now to be a promising source of lithium. But the amount of lithium in that country, as well as how it would be collected and produced remains a mystery.
“When you hear about Afghanistan or Bolivia being huge sources of lithium,” said McKenna, “well they may be someday, but they have a lot of challenges before they get there. Not the least of them, for Bolivia, is that the temperatures are colder and the dryness is not what it is in the Nevada desert or in Chile.”
High-grade batteries and the lithium needed to produce them are not a solution in a vacuum. Rather, they have their own set of political, economic, and ecological considerations that will determine the scale and scope of their success if fully adopted by the transportation industry.