If Aluminum Foil And Bubble Wrap Had A Baby…
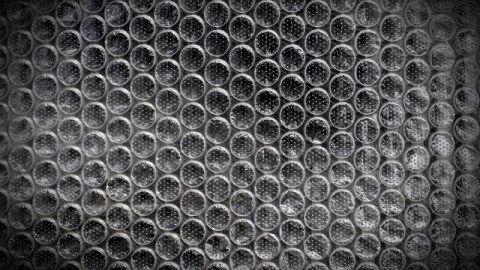
What’s the Latest Development?
Afsaneh Rabiei, a professor of mechanical and aerospace engineering at North Carolina State University, took a thin sheet of aluminum, created small indentations in it, and added a foaming agent in order to create bubbles within them. She then added another layer of aluminum, bonded them together, and put the whole thing in a furnace, where the heat changed the foamy bubbles to air pockets. The resulting material, a kind of metallic bubble wrap, weighs 20 to 30 percent less and is 30 to 50 percent more flexible than an untreated aluminum sheet.
What’s the Big Idea?
The material combines the best properties of sheet metal and bubble wrap: In addition to being lighter and stronger than sheet metal, it’s much more resistant to heat and chemicals than traditional bubble wrap, and can be used to help reinforce thin spaces in items ranging from airplane wings to computer cases. Rabiei says the process can be applied to any sheet metal, and because it’s relatively simple, it’s also low in cost. Her presentation at last month’s International Conference on Porous Metals and Metallic Foams was chosen by the audience as one of the technical highlights of the event.
Photo Credit: Shutterstock.com