‘Fly something else’: Former Boeing manager refuses to fly on the 787 Dreamliner
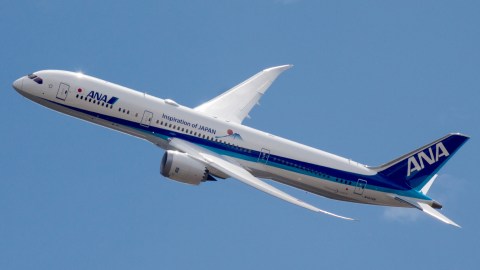
- John Barnett worked as a quality manager at Boeing for three decades, but recently left the company due, in part, to his concerns over issues in the production of the 787 Dreamliner.
- In a recent interview with Corporate Crime Reporter, Barnett said he would “change flights before I would fly a 787. I’ve told my family — please don’t fly a 787.”
- The allegations follow up two 737 crashes that occurred earlier in 2019, calling into question the airline company’s dedication to safety standards.
The past few years have not been good for Boeing. First, in October of 2018, a 737 Max crashed just after take-off from Jakarta, killing 189 people. Then again, in March, another Max flight crashed after take-off in Addis Ababa, Ethiopia, killing 157 people. Ensuing reviews revealed that the Boeing failed to adequately train its pilots on a new system responsible for the crash, refused to install safety systems that could have mitigated the crashes, and even pushed for laws that would cut back on oversight.
Now, a former quality manager for Boeing explained in a recent interview with Corporate Crime Reporter why these issues aren’t limited to just the 737, and why he refuses to fly on Boeing’s 787 Dreamliner.
Lowered safety standards
John Barnett had been a quality manager for Boeing for three decades, work which he enjoyed until he was transferred to Boeing’s plant in Charleston, South Carolina, where the 787 is manufactured. Soon after his arrival in 2010, a new leadership team whose previous experience centered on Boeing’s military projects began overseeing work on the commercial airliner at the plant.
“They started pressuring us to not document defects,” said Barnett, “to work outside the procedures, to allow defective material to be installed without being corrected. They started bypassing procedures and not maintaining configurement control of airplanes, not maintaining control of non-conforming parts — they just wanted to get the planes pushed out the door and make the cash register ring.”
At first, Barnett claims, these lapses started out as administrative issues, such as encouraging workers to improperly fill out paperwork. “Over time it got worse and worse,” he said. They began to ignore defective parts installed on the planes and basic issues related to aircraft safety.
For example, one audit uncovered that approximately 25 percent of oxygen masks didn’t work. Defective parts became lost in the system, only to be later discovered installed on flying aircraft. Barnett particularly recalls several defective bulkheads being installed without having been repaired.
Another major issue were the metal slivers. When securing the plane’s floorboard with titanium fasteners, 3-inch-long slivers of razor-sharp metal would fall down into the compartment where the aircraft’s sensitive electronic equipment lies.
“That surface below the floor board is where all of your flight control wires are, that’s where all of your electronic equipment is,” said Barnett. “It controls systems on the airplane, it controls the power of the airplane. All of your electronic equipment is down where all of these metal slivers are falling.” Even at the Charleston plant, Barnett described how these slivers would cause electrical shorts and start fires. As the planes vibrate, these metal slivers eventually work their way into the wire bundles and connectors with the potential to cause these issues during flight.
I want the people to know what they are riding on.
Barnett filed complaints with multiple members of the Boeing team, which he asserts resulted in his reassignment to a stand-alone department that isolated him from other quality managers. The Federal Aviation Administration (FAA) did come in and do an audit, substantiating Barnett’s claims. As a result of this, the FAA told Boeing that no more planes could be delivered that contained those metal slivers. However, Boeing had determined that the metal slivers were not a safety issue on the planes they had already delivered, and so the customers did not need to be informed. “And at the time,” said Barnett, “I think we were up around 800 airplanes that had been delivered. Every 787 out there has these slivers out there.”
Without seeing significant improvements, Barnett filed a complaint with the Occupational Safety and Health Administration (OSHA) in January 2017. As of this writing, OSHA is still investigating and has not made any determinations.
Barnett stressed that he was a fan of Boeing’s planes overall, asserting that the previous planes he worked on were built to be safe and airworthy. “But as far as the 787, I would change flights before I would fly a 787. I’ve told my family — please don’t fly a 787. Fly something else. Try to get a different ticket. I want the people to know what they are riding on.”
Wreckage from the March 2019 crash of a 737 Max airliner outside of Addis Ababa, Ethiopia.
Xinhua/ via Getty Images
Lowering the regulatory bar
These allegations add on to previous criticisms that the airline company is putting profit ahead of safety as a means of staying ahead of its major competitor, Airbus. Together, they effectively form a duopoly in the airline industry, and staying ahead of its competitor in the already challenging industry has pushed Boeing to cut corners. Critics assert that the company intentionally skipped training pilots in new systems and procedures, a decision which may have led to the two 737 crashes earlier in 2019 and 2018.
Compounding these issues, the company has successfully lobbied for reduced oversight as well. The most recent manifestation of this was Boeing’s lobbying efforts toward the FAA Reauthorization Act of 2018, a bill that the FAA claimed would “not be in the best interest of safety.” A former FAA attorney claimed that “it set the FAA up for being totally deferential to the industry.” Coupled with Barnett’s claims that the company has been ignoring quality concerns in the 787 Dreamliner and the 737’s recent crashes, this hamstrung regulatory environment does not inspire confidence.